The Impact of Recasting on the Bond Strength of Metal Ceramic Restorations
Abstract
Objective
The objective of this study is to evaluate the effect of recasting of Nickel Chromium (Ni-Cr) alloy on the bond strength of metal-ceramic restoration.
Materials and Methods
Forty-five samples fabricated from one Ni-Cr alloy were divided into three groups. Group 1 consisted of 100% fresh alloy; Group 2 consisted of 50% fresh alloy mixed with 50% alloy taken from sprue and button remnants of group 1 and group 3 consisted of 50% new alloy mixed with 50% alloy taken from sprue and button remnants of group 2. All samples were then bonded to a ceramic material. The bond strength of the Metal-Ceramic was then assessed using a 3-point bending test. The failure mode was investigated under a stereomicroscope and confirmed under scanning electron microscopy (SEM).
Results
Group 1 (100% fresh alloy) showed the highest bond strength amongst the other groups, while the lowest was recorded for group 3 (50% fresh alloy with 50% cast twice alloy). According to the International Organization for Standardization (ISO), the bond strength of fresh alloy and the group casted once attained the required level.
Conclusion
The outcome of this study indicates that the use of 100% fresh Ni-Cr base metal alloy yields the highest bond strength of metal ceramic restoration.
1. INTRODUCTION
Metal-ceramic restorations using base metal alloys continue to be utilized in prosthodontics due to their superior mechanical properties and low cost when compared with gold based alloy [1]. The long-term success of metal-ceramic restorations is dependent on establishing the strongest bond attainable between the metal substructure and the veneering ceramic. A number of factors influencing the bond strength of metal-ceramic restorations have been documented in the literature, as have several mechanisms that contribute to this bond [2].
Additional research has indicated that casting and recasting may produce microstructural defects consisting of cracks and porosity [3]. This is primarily caused by the potential of recasting to change the chemical composition of alloys and consequently the alloys’ properties by altering the amount and/or distribution of elements during the casting process [4]. Moreover, recasting of alloys may also influence the composition and thickness of oxide layers at the metal-ceramic interface [5]. A number of researchers evaluated physical and mechanical properties of metal ceramic restorations such as marginal fit [6], castability [7], surface roughness [8], and hardness [9], whereas other researchers evaluated metal ceramic bond strength [10, 11], and sometimes especially on implant rehabilitations the possibility of obtaining notable results, using temporary cements for cementation, capable of allowing the disassembly of the prosthesis, and avoiding biological problems of all kinds [12]. The effect of recasting on biocompatibility and corrosion was also investigated previously [13].
The strong bond between porcelain and metal is an essential element to guarantee service longevity and clinical performance of metal-ceramic restorations [14]. The recasting of alloys was thought to alter the composition and thickness of the metal oxide layer at the metal-ceramic interface and therefore, the metal-ceramic bond [10, 15]. Numerous studies have also revealed that essential elements such as Cu and Zn may be lost during the casting cycles due to evaporation or oxidation [16]. In order to maintain adequate bond strength, studies suggested that 50% new alloy should be added to previously cast alloy [10].
The controversy remains uncertain, although a previous systematic review indicated that recasting up to four times can only be conducted if each time at least 50% of a new alloy is introduced, however, there has been no introduction of guidelines or consensus [17]. Additionally, due to the divisive nature of the prior studies' findings, the aim of this study was to investigate the impact of recasting base-metal alloy on the bond strength of metal-ceramic restorations and the associated failure modes.
The null hypothesis was that there would be no significant differences in the bond strength of Nickel-Chromium base-metal alloy (Ni-Cr) to the ceramic layer after recasting.
Elements | Mass (%) |
---|---|
Ni | 62.0% |
Cr | 26.2% |
Mo | 9.4% |
Si | 2.4% |
2. MATERIALS AND METHODS
2.1. Sample Size Calculation
The sample size was calculated based on a pilot study using G*Power v3.1 (Heinrich Heine, University of Düsseldorf, Düsseldorf, Germany) with a test power of 0.80 and 5% level of significance. The minimum sample size was established at 10 samples for each group (n=10). For greater reliability and accuracy in the present study, 15 samples per group were used.
2.2. Study Design and Selected Materials
Forty-five test samples were fabricated using the same Nickel-Chromium (Ni-Cr) alloy (Ugirex III, Ugin dentaire, Seyssinet-Pariset, France). The composition and mass content of the used Ni-Cr alloy is presented in Table 1. The samples were divided into three equal groups each consisting of 15 samples. Group 1 (control) consisted of 100% fresh alloy; Group 2 was made up of 50% fresh alloy mixed with 50% alloy from control group’s sprue and button remnants (casted once); and Group 3 consisted of 50% new alloy mixed with 50% alloy from cast once group's sprue and button fragments (casted twice).
Samples in all groups were pre-treated with 250 µm Aluminium oxide (Al2O3) (Cobra, Renfert GmbH, Hilzingen, Germany) and bonded to a conventional ceramic material (Creation CC International GmbH, Meininge, Austria). The physical characteristics of the used ceramic are illustrated in Table 2. Each sample was then subjected to a 3-point bending test using a universal testing machine (Testometric, M350-5CT, Rochdale, UK). A stress-strain curve was produced, and the force leading to ceramic layer debonding was measured in Newton (N).
Property | Measure | Value |
---|---|---|
Dentine Firing | oC | 920 |
Flexural Strength | MPa (N/mm2) | 84 |
Thermal Coefficient | 10.6xK-1 | 13.3+/-0.3 |
Glass Transition Temperature | oC | 580+/-10 |
The tested samples were examined using a stereomicroscope (Leica EZ4 W, Leica Microsystems, Weltzer, Germany), and the mode of failure for each sample was determined and categorized into the adhesive, cohesive, or combined adhesive-cohesive failure. The mode of failure was then confirmed by examining samples under Scanning Electron Microscope (SEM) (VEGA 3 XMU, TESCAN, Kohoutovice, Czech Republic).
2.3. Fabrication of the Experimental Test Samples
The test samples in the present study were prepared in accordance with the International Organization for Standardization (ISO) guidelines for metal ceramic system compatibility testing [18] (Fig. 1).
A cylindrical cast base metal mould with measure-ments of 25 mm (±1 mm), 3.0 mm (±0.1 mm), and 0.5 mm (±0.05 mm) in thickness was designed to standardise the dimensions of 45 fabricated samples (Fig. 2A). A pattern resin (GC AMERICAN INC, IL, USA) was mixed according to the manufacturer's instructions, poured into the mould, and allowed to set (Fig. 2B). The dimensions of each pattern resin sample were measured with a digital caliper (OriginCal IP54 Digital caliper, iGAGING, California, USA) to ensure conformity with the pre-set sample dimensions. Each acrylic resin sample was then prepared for casting by attaching it to a 6mm x 2mm wax sprue at a 45-degree angle. The wax sprues were then attached to a crucible former and fitted into a 55.0mm diameter rubber casting ring, keeping the resin pattern samples at least 2.0mm away from the interior walls and 6.0mm away from the top edge of the ring (Fig. 2C). Each casting ring contained five samples, ultimately a total of nine casting rings were used for the 45 samples. Prior to investing, soft wax was used to secure the seal around the crucible former.
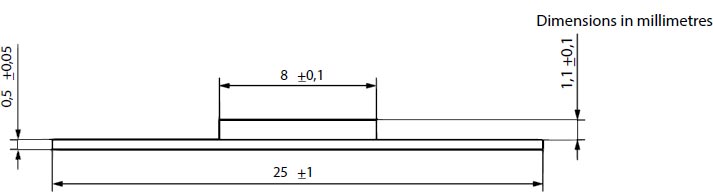
Adapted from ISO 9693-1
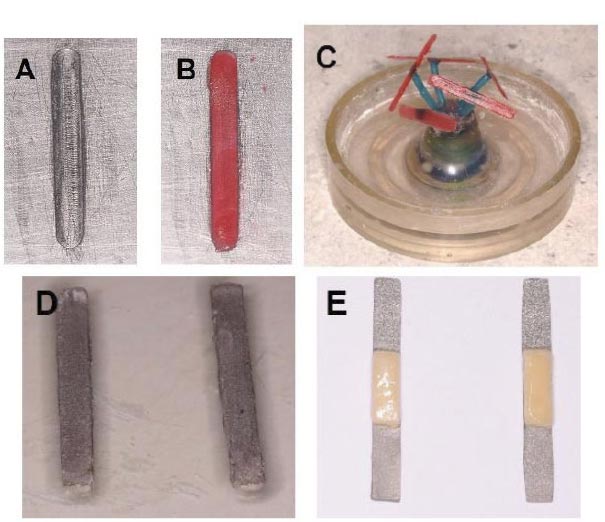
A 160g phosphate-bonded investment powder and a 24ml special liquid from the same manufacturer (Rema CC Kompendium, Dentaurum, GmbH, Germany) were manually mixed for 30 seconds and then mixed for an additional 80 seconds in a vacuum mixer (Twister evolution, Renfert GmbH, Hilzingen, Germany). The mixture was then carefully poured into the casting ring, with low vibration to avoid air entrapment, and the ring was filled to the upper limit.
The investment was kept to set at room temperature for 60 minutes. For group 1 samples, the crucible formers of three rings were removed, with five samples in each ring, and the investment rings were placed in a burnout furnace (PC 30, Ugin Dentaire, Seyssinet-Pariset, France). The furnace temperature was initially set at 290 oC for 30 minutes, then increased to 850oC for 60 minutes as per the manufacturer’s instructions. After the completion of the burn-out cycle, the investment rings were removed from the furnace and cast one at a time in an induction casting machine (Ducatron Quatro, UGIN Dentaire, Seyssinet-Pariset, France).
The formula used to calculate the quantity of alloy required to cast the wax for each casting ring was: W x D= grams of alloy needed, where W is the weight of the resin acrylic patterns with wax sprues in each ring and D is the density of the Ni-Cr alloy as provided by the manufacturer. The weight of the five samples in each ring was measured at 1.0g using a portable weighing scale (Ohaus HH120D-0W0, OHAUS, Pioneer, USA), and the density of the alloy was 8.1g/cm3, as stated by the manufacturer.
Two 6.3 g ingots of 100% new Ni-Cr alloy were used. The additional alloy was added to ensure an adequate metal reservoir to produce sprue buttons for group 2 samples. The ingots were placed in the induction machine's ceramic crucible and heated to 1342 oC as per the manufacturer's instructions. The ring was centrifuged to complete the full casting cycle and then was left to cool for 24 hours on the bench.
This process was repeated for each of Group 1's three rings. The castings were then divested from the rings and sandblasted with 250 µm Aluminium oxide (Al2O3) (Cobra, Renfert GmbH, Hilzingen, Germany) using the sandblasting machine (Basic master, Renfert GmbH, Hilzingen, Germany) to remove any debris. Using laboratory sectioning discs, the samples were separated from their sprues and buttons. The sprues and buttons were sandblasted once more, steam cleaned, and then cut into small segments and weighed for group 2 sample manufacturing. For group 2, three rings were casted in a similar manner as outlined for group 1 samples, with the exception that the alloy used was 50% fresh Ni-Cr alloy mixed with 50% by weight from sprue and button remnants of group 1 castings (cast once alloy). The process for group 3 was carried out in a comparable manner; the remaining three casting rings with the sum of 15 samples were casted using 50% fresh Ni-Cr alloy combined with 50% by weight sprue and button remnants from group 2 castings (cast twice alloy). Following the completion of the casting processes, the dimensions of all test samples were verified using a digital caliper (OriginCal IP54 Digital caliper, iGAGING, California, UAS) to ensure conformity with the pre-set dimensions prior to the ceramic application (Fig. 2D).
The metal substructure was first pre-treated by air blasting with 250 µm Aluminium oxide (Al2O3) (Cobra, Renfert GmbH, Hilzingen, Germany) in the sandblasting machine (Basic master, Renfert GmbH, Hilzingen, Germany) followed by steam cleaning to eliminate impurities. The ceramic (Creation CC International GmbH, Meininge, Austria) was built up using a free-hand layering technique and standard procedures. A symmetrical application of opaque ceramic over a length of 8±0.1 mm was made on one 3 mm-wide edge of each specimen. After firing, dentine ceramic was applied to each specimen, resulting in a total ceramic thickness of 1.1 ± 0.1 mm (Fig. 2E).
The ceramic body layer was originally over-built, then grinded with specialized finishing burs (Porcelain set-1553, NTI-Kahla GmbH, Kahla, Germany) resulting in a final porcelain layer thickness of 1.1 ± 0.1 mm. Glazing was achieved with a brush-on technique and fired at 500oC for 20 minutes.
2.4. The 3-point Bending Test
A custom-made stainless-steel base with two vertical arms 20mm apart from the centre of each other was fabricated to hold and support the sample during the testing procedures. The stainless-steel base was attached to the base of a universal testing machine (Testometric, M350-5CT, Rochdale, UK). The test sample was placed at the centre of the stainless-steel base with the ceramic layer facing downward. For load application, a stainless-steel rod with a flat tip 3.0mm wide and 1.0mm thick was attached to the upper component of the Universal testing machine.
A vertical load force perpendicular to the sample's centre was applied at a constant crosshead speed of 1.5mm/min and recorded until failure. A similar crosshead speed was used previously in studies investigating the effect of alloy’s recasting on bond strength to ceramics [10, 11]. The load to failure curve was generated automatically by the analysis software integrated into the universal testing machine (WinTest-Analysis EC Testing Software, Testometric, Rochdale, UK) and the force required to cause bond failure/fracture was measured in Newtons (N). Fig. (3) illustrates the 3-point test configuration.
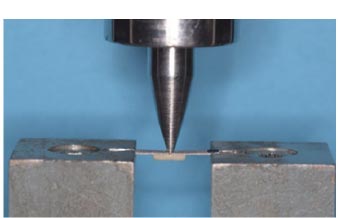
2.5. Calculation of Bond Strength
The debonding/crack-initiation strength (τb) was calculated according to ISO 9693-1 [18] using the following equation: τb = k × F fail.
where F fail is the maximum failure force, and k is a coefficient calculated from the thickness of and the elastic modulus of the metal alloy used.
2.6. Failure Mode Analysis
Each sample was examined under a stereomicroscope (Leica EZ4 W, Leica Microsystems, Weltzer, Germany) equipped with an 8X magnification digital camera (Leica EZ4 D, Leica Microsystems, Weltzer, Germany) to identify the type of bond failure. Each sample was secured at the stereomicroscope's base with utility wax, with the ceramic-metal interface facing the microscope's lens. To identify the type of failure, the area of interest where the failure occurred was focused on and examined under high magnification. Each sample's bond failure was classified as one of three types: adhesive, cohesive, or mixed adhesive-cohesive failure. Complete separation of the porcelain layer from its metal substructure is referred to as adhesive failure. Cohesive failure, on the other hand, signifies fracture within the ceramic layer, whereas combined adhesive-cohesive failure denotes the presence of both types of failures within the same test sample. Mode of failure was checked twice by the same operator with two-week interval.
Samples were then prepared by applying an additional thin layer (10nm) of a conductive material such as gold (sputter coater) in order to be examined under SEM (VEGA 3 XMU, TESCAN, Kohoutovice, Czech Republic).
2.7. Statistical Analyses
The load to fracture data for all groups was checked with Shaprio-Wilk test for normality and analysed and compared using one-way analysis of variance (ANOVA) on the SPSS statistical software program (SPSS version 21, 64-bit edition, IBM, USA). To determine statistical differences between groups, the Tukey HSD post hoc test was used, with the level of significance set at p<0.05. The mode of failure within and between groups was represented as a percentage. The Chi-square test was used to analyse and assess differences in failure mode between groups (p<0.05). Kappa statistics were primarily utilized to evaluate intra-examiner agreement.
3. RESULTS
3.1. Load to Fracture Force
A total of 45 samples were tested (15 for each group) under tensile force to determine the force required to cause failure. The debonding (τb) values were recorded for all groups, where group 1 (100% fresh alloy) revealed the highest debonding value with 60.67 (± 5.84) MPa, while the lowest was recorded for group 3 (50% fresh alloy with 50% cast twice alloy) and measured 24.15 (±4.94) MPa. On the other hand, the load to fracture for group 2 (50% fresh alloy with 50% cast once alloy) was 45.76 (±4.49) MPa. Descriptive statistics of debonding data for all groups are illustrated in Table 3. Mean (SD) of all groups were presented against the ISO recommendation in Fig. (4). The normality of data was checked with Shaprio-Wilk test which revealed no statical difference (p>0.05), indicating the data was normally distributed. Analysis of variance (ANOVA) revealed significant differences between the three groups (p<001). Tukey HSD post hoc test revealed that the debonding value for group 1 was significantly higher than that for groups 2 and 3 (p<001). Similarly, the debonding value for group 2 was significantly higher than that of group 3 (p<001).
3.2. Mode of Failure
The mode of failure was assessed for all 45 samples across the three groups. The types of failures were categorized as adhesive, cohesive, or combined adhesive-cohesive failure and presented by percentages for each group in Table 4. For group 1 (100% fresh alloy), the adhesive failure (Fig. 5A) accounted for 40% (n=6) of all failures, while cohesive failure (Fig. 5B) and combined failure (Fig. 5C) represented 33.3% (n=5) and 26.7% (n=4), respectively. For group 2 (50% fresh alloy with 50% cast once alloy), 73.3% (n=11) of the samples showed adhesive failure while the remaining 26.7% (n=4) showed a combined adhesive-cohesive failure. No cohesive failures were encountered in this group. For group 3 (50% fresh alloy with 50% cast twice alloy), 93.3% of the samples (n=14) exhibited adhesive failure, while only 6.7% (n=1) had a combined adhesive-cohesive failure. Similar to Group 2, no cohesive failures were present in Group 3. In-between group analysis revealed significant differences in the mode of failure (Chi-Square test, p=0.0004), as depicted in Table 4. The kappa test showed 68% intra-examiner agreement on the mode of failure.
Groups | Group 1 (Control) | Group 2 (Casted Once) | Group 3 (Casted Twice) |
---|---|---|---|
Minimum | 53.42 | 39.51 | 16.49 |
Maximum | 75.24 | 52.44 | 36.48 |
Median | 58.84 | 44.39 | 23.218 |
Mean (SD) | 60.67 (5.84)A | 45.76 (4.49)B | 24.15 (4.94)C |
Different superscript letters indicate statistically significant differences (p<001). |
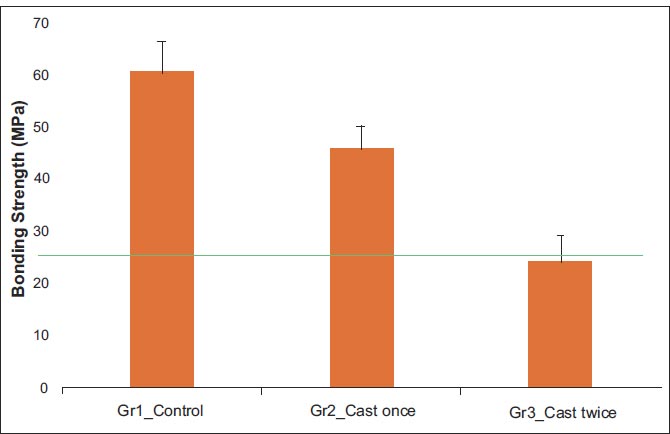
Green line is the ISO recommendation of 25 MPa.
Group | Data | Cohesive | Adhesive | Combination |
---|---|---|---|---|
Group 1 | Count | 5 | 6 | 4 |
% within Group | 33.3% | 40.0% | 26.7% | |
Group 2 | Count | 0 | 11 | 4 |
% within Group | 0.0% | 73.3% | 26.7% | |
Group 3 | Count | 0 | 14 | 1 |
% within Group | 0.0% | 93.3% | 6.7% |
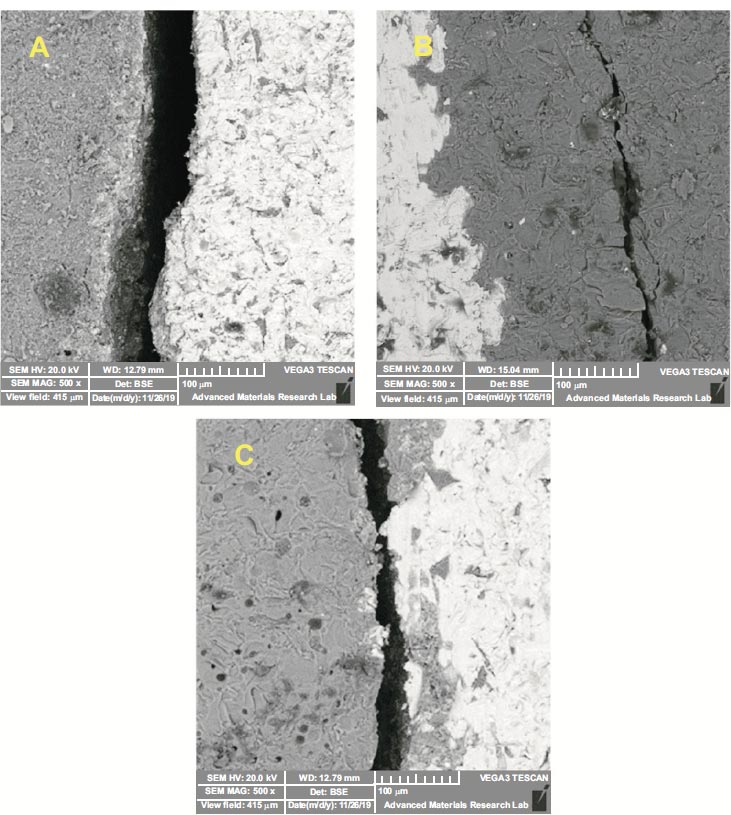
4. DISCUSSION
The aim of the current study was to investigate the effect of recasting of metal alloys on bond strength between metal alloy and ceramics. The results revealed that recasting Ni-Cr alloy once decreased the bond strength significantly. Moreover, the recasting twice dramatically reduced the bond strength between ceramic and Ni-Cr alloy, thus the null hypothesis was rejected.
In the current study, the highest bond strength of 60.67 (± 5.84) MPa was obtained when a 100% fresh alloy was used in group 1. When a 50% recast once alloy was used in Group 2, the bond strength decreased significantly to 45.76 (±4.49) MPa, representing a loss of approximately 25% of the original bond strength. When a 50% recast twice alloy was used in Group 3, the bond strength decreased even further, measuring only 24.15 (±4.94) MPa, or 60% of the bond strength of the 100% fresh alloy.
The result of the current study is in agreement with a previous study which Atluri et al. described a substantial decrease in the metal-ceramic bond strength of Ni-Cr and Co-Cr alloy after multiple recasting [19]. Alturi et al. explained the reason in the reduction of bond strength which could be due to the increase in interfacial void density [19].
Another previous study, in accordance with the result of the current study, compared the bond strength of 100% fresh Ni-Cr alloy to that of 50% fresh alloy mixed with 50% recycled alloy for metal ceramic restorations [10]. Ucar et al. revealed that the bond strength of the ceramic of 100% fresh alloy was significantly higher than that of recycled alloy [10]. The reduction in bond strength could be due to the instability of the composition of alloy and changes in trace elements after recasting [11, 20]. Another study showed similar findings that fresh alloy had the highest bond strength compared to the recast alloy and determined that adding 50% recast alloy reduces the bond strength of the base metal alloy to the ceramic veneer significantly [21]. Some authors suggested when it is necessary to perform casting, it should be mixed with at least 50% fresh alloy to maintain satisfactory bond strength [22]. Walczak et al’s. suggestion was not confirmed specially in Group 3, where the bond strength was 24.15 (±4.94) MPa which is less than ISO Recommendation of bond strength between ceramic and metal alloy which should be at least 25 MPa [18].
The adhesive failure was the most prevalent mode of failure observed across all groups, accounting for nearly 70% of all failures. The greatest number of adhesive failures occurred in Group 3, where 50% of the alloy was a cast alloy with the lowest bond strength measured. On the other hand, the group with the least adhesive failures was group 1, which used only fresh metal alloy. These findings suggest that the stronger the bond between the metal substructure and the ceramic veneer, the less likely adhesive failures are. Only group 1 demonstrated all types of failure modes, with a relatively even distribution across the 15 samples. There is no apparent justification, but one might speculate that when there is a strong bond between the metal and the ceramic, the odds of failure appear to be equal among the various types. Another intriguing finding was that all cohesive failures clustered in group 1, which had the highest bond strength of the three groups. No cohesive failures occurred in groups 2 and 3 could be due to the weaker bond strength in these groups, and this enabled adhesive failure at the interface well before any cohesive failure could be initiated within the ceramic layer. The adhesive failure was increased with the number of recasting, being more in group 3 (recasted twice) than the other groups. It is suggested that the recasting of alloys was thought to alter the composition and thickness of the metal oxide layer at the metal-ceramic interface and therefore, the metal-ceramic bond [10, 15]. The intra-examiner agreement was 68% [23].
The 3-point bending test performed in the current study is similar to the methods used in other recent studies [8, 24] which were all according to ISO 969324. There are other previous studies evaluated the bond strength using the shear bond test [15, 25]. There was no agreement between the results obtained from the two different methods [26].
The practice of recasting base metal alloys to reduce production costs of metal ceramic restorations has been criticized because it does not provide significant financial benefits [27]. The detrimental impact of recasting base metal alloys on the bond strength of metal ceramic restorations certainly outweighs any anticipated financial benefits. This could be an adequate justification because the cost of base metal alloys is relatively inexpensive, making the cost-effectiveness of recasting minimal. Furthermore, the premise that recasting base metal alloys would preserve natural resources and protect the environment [28] could be challenged on the rationale that recasting base metal alloys has been shown to release elemental products with varying levels of toxicity, which increases with the number of recasting cycles [29].
The result of the current investigation supported the notion that the use of fresh metal alloys in metal ceramic restorations would provide a significantly stronger bond between ceramic and metal alloy and positively influence the longevity of the metal ceramic restoration. Furthermore, the use of a mixture of 50% fresh alloy and 50% casted once alloy would grant an adequate bond strength between metal alloy and ceramic greater than the ISO recommendation of 25 MPa. These outcomes confirmed previously published results [10].
In fact, the present report evaluated the bond strength and failure mode of metal ceramic restorations. However, in the past, many studies have been conducted with composite restorations evaluating optical properties [30], surface roughness [31] and wear [32].
Analysis of metal-ceramic restorations in the future is crucial. It could be attempted to compare the physical and mechanical properties of these restorations after casting and sintering with tooth-colored restorations such as composites and all ceramic restorations. Several factors that simulate clinical condition such as complex and multidirectional forces of the oral environment and the influence of saliva and humidity and aging on the bond strength, could be considered limitations of the present study as they were not investigated.
CONCLUSION
With the limitations of the current study, the following conclusions were drawn:
1. The use of 100% fresh Ni-Cr base metal alloy produced the maximum bond of metal ceramic restoration.
2. The mixture of 50% fresh alloy and 50% casted-once alloy provided adequate bond strength between metal and ceramic.
3. The use of multiple recasted alloy resulted in weak bond between metal and ceramic.
LIS OF ABBREVIATIONS
Ni-Cr | = Nickel-Chromium |
SEM | = Scanning Electron Microscopy |
ISO | = International Organization for Standardization |